“La fabbrica del futuro sarà senza uomini, allo stesso modo in cui gli uffici oggi sono senza carta”. La riflessione è di un top manager tedesco che Industry 4.0 la conosce bene: Bernhard Diegner, Production Engineering at ZVEI Services GmbH.
E un altro tedesco, Bernhard Konzet, amministratore delegato della Blulink di Reggio Emilia che produce software mirati al controllo della qualità e della sicurezza sul lavoro nell’era digitale aggiunge: “Non credo che esista davvero la fabbrica totalmente digitale ‘già pronta’. C’è molta fantascienza in questa materia, troppa. Credo però che siamo “in marcia”. Tante cose che fino a qualche anno fa credevamo impossibili oggi sono opportunità concrete, sono possibili. La tensione nelle aziende aumenta perché ormai tutti capiscono che qualcosa si deve fare”.
Ma cosa?
Prima certamente è necessario aver fatto altri “passi”: introdurre il Lean, ad esempio, per rendere la fabbrica snella eliminando gli sprechi. Prima ancora di renderla “digitale”.
Quindi avremo i “Robot al potere”?
“Nemmeno per sogno, anzi saranno sempre di più i cervelli a far funzionare le aziende, a renderle vincenti”. Su questo concordano decine di analisi su scenario più o meno catastrofici in relazione alla perdita di posti di lavoro che l’automazione industriale 4.0 potrebbe creare.
L’aspetto umano rimane centrale anche nella nuova fabbrica digitale e flessibile, che si caratterizzerà per un flusso di comunicazione interno in tempo reale fra le postazioni di lavoro, tale da consentire la capacità autodiagnostica e il controllo a distanza della produzione, in cui la flessibilità dei sistemi permetterà di personalizzare i prodotti in funzione della domanda, e la catena di produzione sarà ricostruita e simulata in un ambiente virtuale, per testarla, per risolvere i problemi a monte e consentire l’addestramento del personale.
E’ invece vero, verissimo che la formazione tecnica di quadri e dirigenti rimane ancora il punto debole per un avvio veloce di Industria 4.0, la digitalizzazione dei processi industriali, soprattutto nel manifatturiero.
A che punto siamo in Italia?
Se da un lato è vero che il 39% delle aziende sta lavorando concretamente sul tema della digitalizzazione (si parla del doppio rispetto al 2015), è altrettanto vero però che il 23% non si è mai occupato di Industria 4.0.
Di certo è iniziata una fase di investimenti, anche grazie alla manovra Industry 4.0 del Governo che offre vantaggi fiscali notevoli.
I nuovi investimenti sono in arrivo in particolare nel comparto dei macchinari (+13% le commesse interne delle associazioni federate in Federmacchine) e di tutte le attività legate alla loro connessione, controllo e manutenzione.
Anche in questo caso però c’è un “difetto italiano”.
“Non basta comprare automazione perché ci sono gli sgravi fiscali (l’iperammortamento) – spiega Luca Pietranera – serve una Vision, un progetto di crescita prima di avviare la digitalizzazione dell’azienda. E troppi imprenditori questa Vision strategica proprio non l’hanno maturata”.
Con il piano Calenda di incentivi all’industria 4.0, il manifatturiero italiano può davvero fare un salto tecnologico verso la quarta rivoluzione industriale, colmando il gap attuale che vede in media macchine utensili vecchie di 15 anni negli impianti produttivi (secondo Ucimu).
Appare chiaro a molti, ma non a tutti che per comprendere la cosiddetta quarta rivoluzione industriale dobbiamo mettere sotto la lente l’intera impresa. La rivoluzione, quella vera, è fatta da cambiamenti repentini del modo di competere sul mercato. Di conseguenza, per fare la rivoluzione non si parte dalla tecnologia, ma dalla strategia.
A monte e a valle della produzione, infatti, un’azienda che sta facendo investimenti tecnologici (siano essi revamping o installazione di nuovi impianti) è chiamata alla sfida dell’innovazione organizzativa, per mettere a frutto il forte cambiamento imposto da sfide come l’IoT (Internet of Things), l’intelligenza artificiale e quella adattativa delle linee produttive, l’interazione fra i robot antropomorfi e gli operai, l’integrazione con i fornitori, i distributori e i clienti finali.
“L’introduzione delle tecnologie della quarta rivoluzione industriale deve essere al servizio di processi e procedure “ripensati e ripuliti dagli sprechi” attraverso un cambiamento della cultura aziendale che dovrà però avere sempre come riferimento la “valorizzazione e la crescita delle persone”, avverte Matteo Bonfiglioli che vede Industry 4.0 con molti anni di esperienza sul Lean Thinking.
Il guru della Tps: il Sensei (che vuol dire maestro) Satoshi Kuroiwa non si stanca di ripetere che non si può entrare nell’era 4.0 saltando fasi evolutive importanti e che la porta d’ingresso è il Tps (Toyota production system).
Il rischio, in buona sostanza, è interpretare questa quarta rivoluzione industriale solo come digitalizzare, robotizzare ed automatizzare delle imprese, con la possibilità di ripercorrere il fallimento del CIM (Computer Integrated Manufacturing) degli anni ’90.
I ROBOT AL POTERE? NEMMENO PER SOGNO
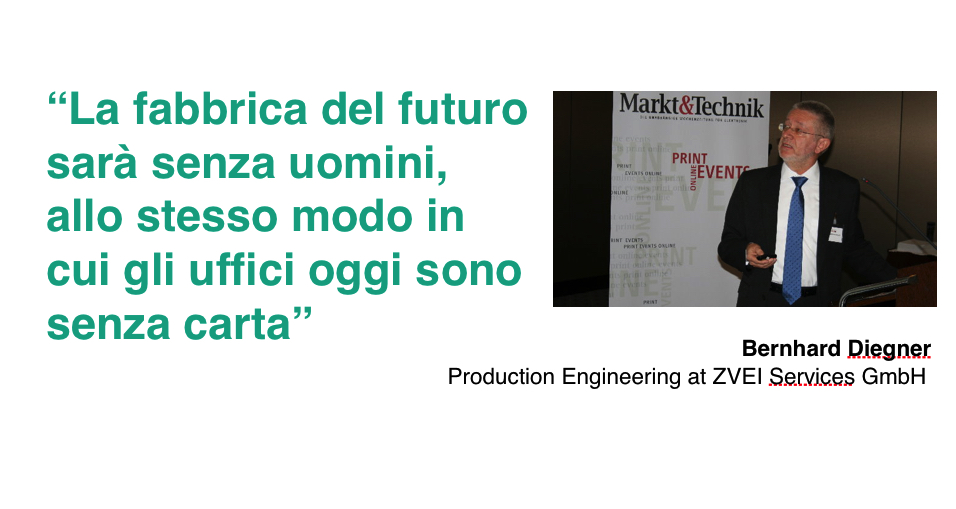